快速成型技术的特点与不足
众所周知,快速成型技术大大节约了制作时间和降低生产成本,那的优点与传统工序来讲,快速成型技术的应用就快速成型技术的特点与不足。
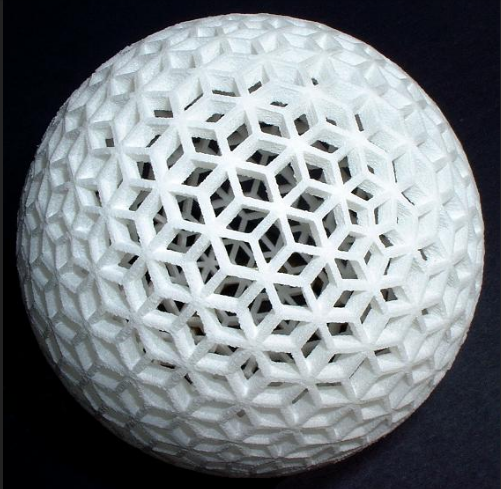
主要体现在如下几个方面:
1)新产品研发过程中的设计验证。
RP工艺缩短了产品研发周期,快速响应市场需求。传统的新品试制过程,用户往往需要耗时3~5个月新品的首批样件。引入RP技术,技术员能在短周期(几小时或几天)内加工出产品原型。
2)工艺性能与装配性能验证。
工艺性能和装配性能对于产品的最终技术路线制定至关重要。对于空间比较复杂的结构系统,如机车、武器装备、医疗器械的加工工艺性和装配性采用RP技术制造原型进行分析和验证。
3)单件、小批量和非标准零部件加工。
对于单件、小批量和非标准零部件的生产,往往没有通用的刀具、夹具、辅具和量具,采用熔融快速成型技术直接制造高强度的工程塑料零部件,满足工业场合应用要求。这种加工方法对于航空及国防工业具有重
要意义。
4)快速模具制造。
采用选择性激光烧结(SLS)、熔融沉积制造(FDM)和叠层实体制造(LOM)等工艺能够直接生产出合金模、树脂模、陶瓷模和金属模等模具。主要优点是制模的工艺相对简单、成型精度高且工期短。
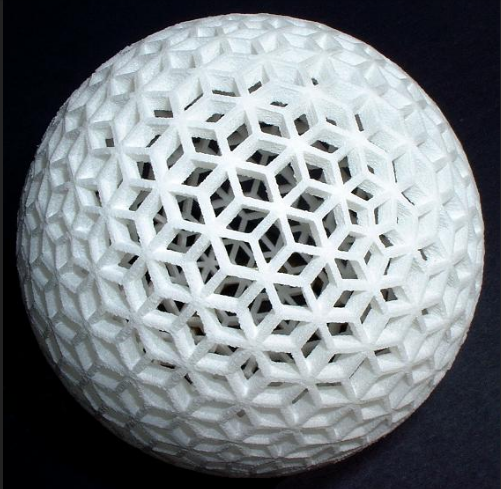
主要体现在如下几个方面:
1)新产品研发过程中的设计验证。
RP工艺缩短了产品研发周期,快速响应市场需求。传统的新品试制过程,用户往往需要耗时3~5个月新品的首批样件。引入RP技术,技术员能在短周期(几小时或几天)内加工出产品原型。
2)工艺性能与装配性能验证。
工艺性能和装配性能对于产品的最终技术路线制定至关重要。对于空间比较复杂的结构系统,如机车、武器装备、医疗器械的加工工艺性和装配性采用RP技术制造原型进行分析和验证。
3)单件、小批量和非标准零部件加工。
对于单件、小批量和非标准零部件的生产,往往没有通用的刀具、夹具、辅具和量具,采用熔融快速成型技术直接制造高强度的工程塑料零部件,满足工业场合应用要求。这种加工方法对于航空及国防工业具有重
要意义。
4)快速模具制造。
采用选择性激光烧结(SLS)、熔融沉积制造(FDM)和叠层实体制造(LOM)等工艺能够直接生产出合金模、树脂模、陶瓷模和金属模等模具。主要优点是制模的工艺相对简单、成型精度高且工期短。